The sustained spike in global energy prices has put utility consumption within the professional textile care industry firmly into the spotlight. With no respite in sight, what can owners and operators do to recover their margins? Perhaps the answer is already in front of them. Here, Christine Rush, Global Product Manager – Dryers, looks at the evolution of heat pump technology, and how it could hold the key to combatting the energy crisis.
Using heat pumps within commercial tumble dryers
The use of heat pumps within commercial tumble dryers is not a recent innovation. Indeed, the technology has been deployed for over forty years. While it has retained a loyal customer base, especially in countries where heat pump technology is used in other mainstream applications such as domestic heating; many textile care professionals have been quick to dismiss its use due to several long-standing perceptions.
For those running a commercial laundry, success often equates to productivity. Put simply, the higher the number of daily cycles, the more money that can be made.
While heat pump dryers have often delivered lower running costs compared to vented dryers powered by gas or electricity, they have been unable to deliver even remotely equivalent cycle times. Coupled with a higher purchase price, there is little wonder heat pump dryers have yet to win over large parts of the on-premise laundry (OPL) market.
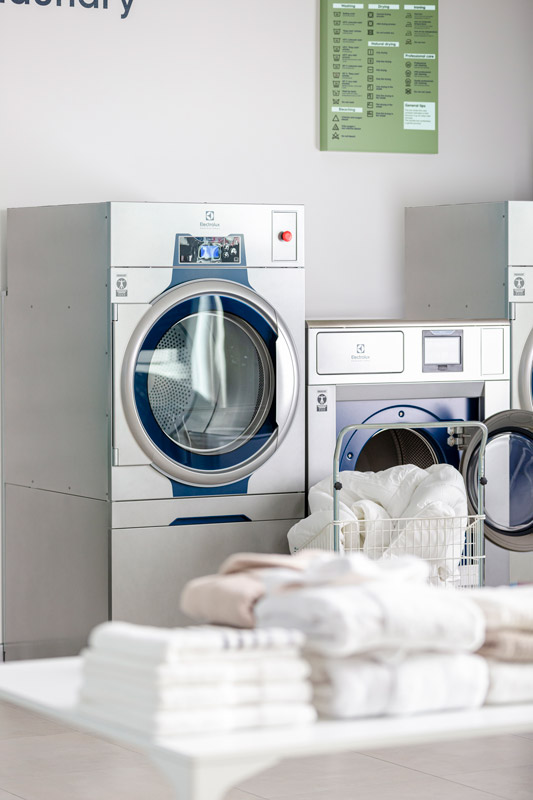
The rising cost of energy
With the sustained spike in prices across the global energy markets, many are starting to think twice about their choice of drying technology. For many years 60% of Swedish commercial tumble dryer installations were heat pump dryers. However, at the end of 2022, that figure rose to 75%. Installation numbers have also grown in France and Germany – in part due to Government subsidiaries for sustainable technologies – as well as other European nations. We have even started to see an upturn in enquires throughout APAC and the US: two regions with a strong install base of vented dryers.
Yet, this should not come as a surprise. Afterall, commercial tumble dryers consume more than three times the amount of energy as a washing machine.
Given the average unit cost of electricity has tripled in the past year, the traditional trade-off of higher OpEx for the faster cycle times of vented dryers has diminished.
How a heat pump dryer makes you save energy
While energy cost is undoubtedly a major factor, so too is innovation. Indeed, modern heat pump dryers – such as those in Electrolux Professional’s Line 6000 series – have made significant headway in overcoming the major barrier to mass implementation: cycle time.
The secret lies in taking inspiration from other heat pump applications. Unlike other models on the market, the Line 6000 heat pump dryer features an inverter-driven compressor and electronic valve within the heat pump unit. Like the technology used in domestic air conditioning or heat pump applications, it significantly reduces temperature fluctuations versus traditional mechanical valve regulation, resulting in better temperature control and faster dewatering.
Not only does this further improve energy consumption, but it changes the game when it comes to cycle times. Now, OPL professionals have access to a heat pump dryer that can run a cycle in 35 mins – just 5 minutes longer than a vented dryer, and nearly twice as fast as traditional heat pump dryers.
The impact of these two factors cannot be overestimated when it comes to evaluating productivity. Compared to a vented dryer, a new heat pump dryer that runs for 3,000 cycles a year will use 65% less energy a year: the equivalent annual energy usage of three traditional family homes.
Coupled with just a five-minute difference in cycle times, OPL professionals now no longer need to trade-off between energy consumption and output. Even when you factor in the slightly higher purchase price of a heat pump dyer, the payback period can be as low as two years; while the lower running costs and comparable cycle times will pay for the unit again and again over a decade or more of operation.
However, while heat pump dryers now represent a sizeable energy-saving opportunity, it is important to contextualise the technology within the overall laundry cycle management process.
To get the best out of a heat pump dryer, it needs to work alongside a high-spin commercial washer. This will maximise dewatering prior to the drying stage and ensure that drying cycles can operate as efficiently as possible.
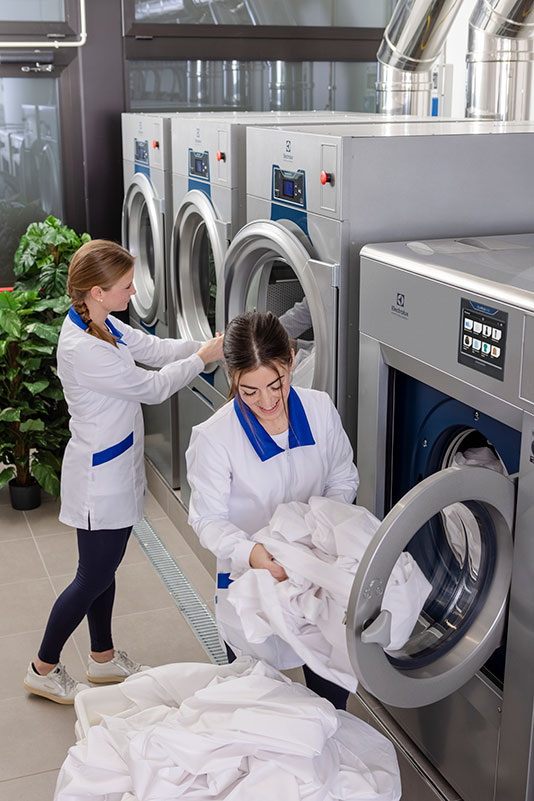
While high-spin washers are the norm for many countries, they are not yet the default choice in others. Therefore, anyone considering investing in a heat pump dryer should also consider their washer units to maximise both energy savings and productivity.
Conclusion
The commercial laundry world is a very different place than it was 12 months ago. With energy prices set to remain high over the coming year and beyond, the case for innovative heat pump dryer technology will only become stronger.